The Controller Area Network (CAN) is a serial bus communications protocol developed by Bosch (an electrical equipment manufacturer in Germany) in the early 1980s. Thereafter, CAN was standardized as ISO-11898 and ISO-11519, establishing itself as the standard protocol for in-vehicle networking in the auto industry. In the early days of the automotive industry, localized stand-alone controllers had been used to manage various actuators and electromechanical subsystems. By networking the electronics in vehicles with CAN, however, they could be controlled from a central point, the engine control unit (ECU), thus increasing functionality, adding modularity, and making diagnostic processes more efficient.
Early CAN development was mainly supported by the vehicle industry, as it was used in passenger cars, boats, trucks, and other types of vehicles. Today the CAN protocol is used in many other fields in applications that call for networked embedded control, including industrial automation, medical applications, building automation, weaving machines, and production machinery. CAN offers an efficient communication protocol between sensors, actuators, controllers, and other nodes in real-time applications, and is known for its simplicity, reliability, and high performance.
The CAN protocol is based on a bus topology, and only two wires are needed for communication over a CAN bus. The bus has a multimaster structure where each device on the bus can send or receive data. Only one device can send data at any time while all the others listen. If two or more devices attempt to send data at the same time, the one with the highest priority is allowed to send its data while the others return to receive mode.
As shown in Figure 9.1, in a typical vehicle application there is usually more than one CAN bus, and they operate at different speeds. Slower devices, such as door control, climate control, and driver information modules, can be connected to a slow speed bus. Devices that require faster response, such as the ABS antilock braking system, the transmission control module, and the electronic throttle module, are connected to a faster CAN bus.
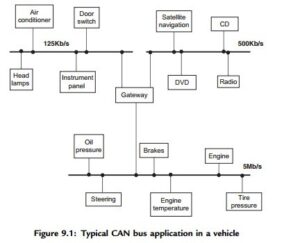
The automotive industry’s use of CAN has caused mass production of CAN controllers. Current estimate is that 400 million CAN modules are sold every year, and CAN controllers are integrated on many microcontrollers, including PIC microcontrollers, and are available at low cost.
Figure 9.2 shows a CAN bus with three nodes. The CAN protocol is based on CSMA/ CDþAMP (Carrier-Sense Multiple Access/Collision Detection with Arbitration on Message Priority) protocol, which is similar to the protocol used in Ethernet LAN. When Ethernet detects a collision, the sending nodes simply stop transmitting and wait
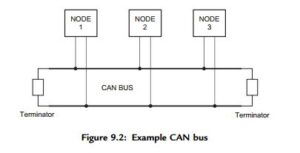
a random amount of time before trying to send again. CAN protocol, however, solves the collision problem using the principle of arbitration, where only the higheest priority node is given the right to send its data.
There are basically two types of CAN protocols: 2.0A and 2.0B. CAN 2.0A is the earlier standard with 11 bits of identifier, while CAN 2.0B is the new extended standard with 29 bits of identifier. 2.0B controllers are completely backward-compatible with 2.0A controllers and can receive and transmit messages in either format.
There are two types of 2.0A controllers. The first is capable of sending and receiving 2.0A messages only, and reception of a 2.0B message will flag an error. The second type of 2.0A controller (known as 2.0B passive) sends and receives 2.0A messages but will also acknowledge receipt of 2.0B messages and then ignore them.
Some of the CAN protocol features are:
• CAN bus is multimaster. When the bus is free, any device attached to the bus can start sending a message.
• CAN bus protocol is flexible. The devices connected to the bus have no addresses, which means messages are not transmitted from one node to another based on addresses. Instead, all nodes in the system receive every message transmitted on the bus, and it is up to each node to decide whether the received message should be kept or discarded. A single message can be destined for a particular node or for many nodes, depending on how the system is designed. Another advantage of having no addresses is that when a device is added to or removed from the bus, no configuration data needs to be changed (i.e., the bus is “hot pluggable”).
• CAN bus offers remote transmit request (RTR), which means that one node on the bus is able to request information from the other nodes. Thus instead of waiting for a node to continuously send information, a request for information can be sent to the node. For example, in a vehicle, where the engine temperature is an important parameter, the system can be designed so the temperature is sent periodically over the bus. However, a more elegant solution is to request the temperature as needed, since it minimizes the bus traffic while maintaining the network’s integrity.
• CAN bus communication speed is not fixed. Any communication speed can be set for the devices attached to a bus.
• All devices on the bus can detect an error. The device that has detected an error immediately notifies all other devices.
• Multiple devices can be connected to the bus at the same time, and there are no logical limits to the number of devices that can be connected. In practice, the number of units that can be attached to a bus is limited by the bus’s delay time and electrical load.
The data on CAN bus is differential and can be in two states: dominant and recessive. Figure 9.3 shows the state of voltages on the bus. The bus defines a logic bit 0 as a dominant bit and a logic bit 1 as a recessive bit. When there is arbitration on the bus, a
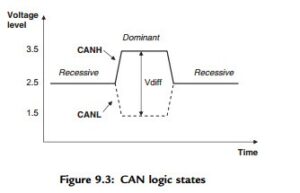
dominant bit state always wins out over a recessive bit state. In the recessive state, the differential voltage CANH and CANL is less than the minimum threshold (i.e., less than 0.5V receiver input and less than 1.5V transmitter output). In the dominant state, the differential voltage CANH and CANL is greater than the minimum threshold.
The ISO-11898 CAN bus specifies that a device on that bus must be able to drive a forty-meter cable at 1Mb/s. A much longer bus length can usually be achieved by lowering the bus speed. Figure 9.4 shows the variation of bus length with the communication speed. For example, with a bus length of one thousand meters we can have a maximum speed of 40Kb/s.
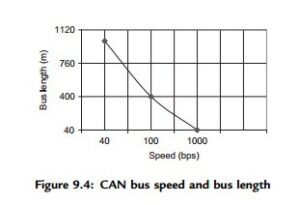
A CAN bus is terminated to minimize signal reflections on the bus. The ISO-11898 requires that the bus has a characteristic impedance of 120 ohms. The bus can be terminated by one of the following methods:
• Standard termination
• Split termination
• Biased split termination
In standard termination, the most common termination method, a 120-ohm resistor is used at each end of the bus, as shown in Figure 9.5(a). In split termination, the ends of the bus are split and a single 60-ohm resistor is used as shown in Figure 9.5(b). Split termination allows for reduced emission, and this method is gaining popularity. Biased split termination is similar to split termination except that a voltage divider
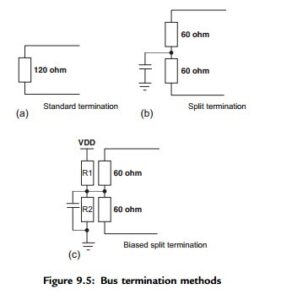
circuit and a capacitor are used at either end of the bus. This method increases the EMC performance of the bus (Figure 9.5(c)).
Many network protocols are described using the seven-layer Open Systems Interconnection (OSI) model. The CAN protocol includes the data link layer, and the physical layer of the OSI reference model (see Figure 9.6). The data link layer (DLL) consists of the Logical Link Control (LLC) and Medium Access Control (MAC). LLC manages the overload notification, acceptance filtering, and recovery management. MAC manages the data encapsulation, frame coding, error detection, and serialization/deserialization of the data. The physical layer consists of the physical signaling layer (PSL), physical medium attachment (PMA), and the medium dependent interface (MDI). PSL manages the bit encoding/decoding and bit timing. PMA manages the driver/receiver characteristics, and MDI is the connections and wires.
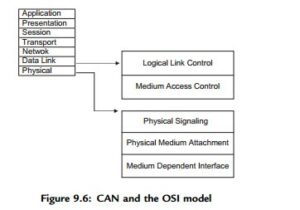
There are basically four message frames in CAN: data, remote, error, and overload. The data and remote frames need to be set by the user. The other two are set by the CAN hardware.